The term "melt shop" might sound niche, but its significance in industries like steel manufacturing, metallurgy, and even culinary arts cannot be overstated. Whether you're a professional looking to refine your understanding or a curious enthusiast, the melt shop has become a vital part of modern industrial processes. It’s where raw materials are transformed into usable forms, laying the foundation for countless products we encounter daily.
Melt shop operations are intricate, involving state-of-the-art technology, skilled labor, and stringent safety protocols. From smelting to casting and refining, a melt shop represents the beating heart of production facilities in metalworking industries. The innovations in melt shop processes have not only increased efficiency but also significantly reduced environmental impacts, making them indispensable in today’s industry landscape.
In this comprehensive guide, we’ll delve deep into what a melt shop is, how it functions, and the roles it plays across various domains. We’ll also explore related technologies, environmental considerations, job opportunities, and much more. If you're eager to learn about this fascinating topic, keep reading to uncover everything you need to know about melt shops.
Read also:Ultimate Style Guide To Cuts Shirt Everything You Need To Know
Table of Contents
- What is a Melt Shop?
- How Does a Melt Shop Work?
- Key Components of a Melt Shop
- What Are the Types of Melt Shops?
- Technologies Used in Melt Shops
- Applications of Melt Shops Across Industries
- What Are the Safety Measures in Melt Shops?
- Environmental Impact of Melt Shops
- How to Optimize Melt Shop Efficiency?
- Job Opportunities in Melt Shops
- Cost Analysis of Melt Shop Operations
- Future Trends and Innovations in Melt Shops
- How to Set Up a Melt Shop?
- Frequently Asked Questions
- Conclusion
What is a Melt Shop?
At its core, a melt shop is a facility where raw metal materials are melted, refined, and cast into specific shapes and forms. These materials can include iron, steel, aluminum, and other alloys, depending on the industry. Typically, melt shops are part of larger manufacturing or steel production plants.
The primary purpose of a melt shop is to facilitate the conversion of raw materials into a usable form through processes like smelting, melting, and refining. This foundational work enables the creation of various products, from construction materials to automotive components.
Melt shops are integral to industries like metallurgy, construction, and even aerospace. Their operations are backed by high-tech equipment and skilled workforce, ensuring the production of high-quality metal products that meet stringent industry standards.
Key Features of a Melt Shop
- Furnaces for melting raw materials
- Refining equipment to remove impurities
- Advanced cooling systems for solidification
- Skilled labor and team operation
How Does a Melt Shop Work?
The operations of a melt shop are a blend of art and science. Each step in the process involves precision and advanced technology to ensure the end product meets quality standards. Here’s an overview of how a melt shop works:
1. Raw Material Collection and Sorting
The process starts with sourcing and sorting raw materials like scrap metal, iron ore, or alloys. These materials are inspected for quality before entering the melting phase.
2. Melting Process
Using furnaces like electric arc furnaces or induction furnaces, the raw materials are subjected to extreme heat to convert them into a molten state. The type of furnace used depends on the specific requirements of the operation.
Read also:The Ultimate Guide To Catch Aria Everything You Need To Know
3. Refining and Alloying
Once the metal is molten, impurities are removed through refining processes. Alloying elements may be added at this stage to achieve the desired material properties.
4. Casting and Solidification
The refined molten metal is then poured into molds or cast into specific shapes. Cooling systems are used to solidify the metal into its final form.
5. Quality Control
After solidification, the metal products undergo rigorous quality checks to ensure they meet the required specifications.
By following these steps, melt shops ensure the production of high-quality materials that cater to various industries.
Key Components of a Melt Shop
A melt shop comprises several critical components, each playing a unique role in the production process. Let’s examine these components in detail:
- Furnaces: These include electric arc furnaces (EAF), induction furnaces, and basic oxygen furnaces, each suited for different types of metals.
- Crane Systems: Used for transporting heavy materials within the shop.
- Cooling Systems: Essential for solidifying molten metals post-casting.
- Control Panels: Advanced systems for regulating temperature, pressure, and other operational parameters.
- Refining Stations: Dedicated areas for removing impurities and adding alloys.
Each of these components contributes to the seamless operation of a melt shop, ensuring efficiency and precision in every step.
What Are the Types of Melt Shops?
Melt shops can be categorized based on the type of metals they process and the technologies they employ. Here are the main types:
1. Steel Melt Shops
These are the most common type and are primarily used for producing steel. Electric arc furnaces and basic oxygen furnaces are typically used in these facilities.
2. Non-Ferrous Melt Shops
These focus on metals other than iron, such as aluminum, copper, and zinc. Induction furnaces are often employed in these shops.
3. Specialty Alloy Melt Shops
These are dedicated to producing high-performance alloys for industries like aerospace and medical equipment. The processes and technologies here are highly specialized.
The type of melt shop depends on the industry requirements and the specific materials being processed.
Technologies Used in Melt Shops
Modern melt shops leverage advanced technologies to enhance efficiency and reduce environmental impact. Some of the key technologies include:
- Automation: Automated systems for material handling and process control.
- Emission Control Systems: To reduce pollutants and comply with environmental regulations.
- AI and Machine Learning: For predictive maintenance and process optimization.
- Energy Recovery Systems: Efficient systems to utilize waste heat generated during operations.
These technologies are transforming melt shop operations, making them more sustainable and efficient.
Applications of Melt Shops Across Industries
Melt shops play a vital role in various industries. Some of the key applications include:
- Construction: Producing steel beams, bars, and other structural components.
- Automotive: Manufacturing engine parts, chassis, and other components.
- Aerospace: Creating high-performance alloys for aircraft and spacecraft.
- Electronics: Providing materials for circuit boards and other electronic devices.
The versatility of melt shops makes them indispensable across these industries.
Frequently Asked Questions
1. What is the purpose of a melt shop?
A melt shop is designed to melt, refine, and cast raw metals into usable forms for various industrial applications.
2. Are melt shop operations environmentally friendly?
Modern melt shops use advanced technologies to minimize environmental impact, such as emission control systems and energy recovery methods.
3. What types of metals are processed in melt shops?
Melt shops handle a variety of metals, including steel, aluminum, copper, and specialty alloys.
4. How are safety measures implemented in melt shops?
Safety measures include protective gear for workers, automated systems, and rigorous adherence to safety protocols.
5. What industries rely on melt shops?
Industries like construction, automotive, aerospace, and electronics heavily rely on melt shops for their operations.
6. Can small-scale businesses set up a melt shop?
Yes, small-scale melt shops can be set up, but they require significant investment in equipment and skilled labor.
Conclusion
The melt shop is a cornerstone of modern industrial processes, enabling the production of high-quality metals and alloys critical to countless industries. With advancements in technology, melt shops are becoming more efficient, sustainable, and versatile, ensuring their continued relevance in the future.
Whether you're interested in the technical aspects, job opportunities, or environmental impact of melt shops, this guide has provided a comprehensive overview. The next time you encounter a product made of metal, you’ll have a newfound appreciation for the melt shop processes that made it possible.
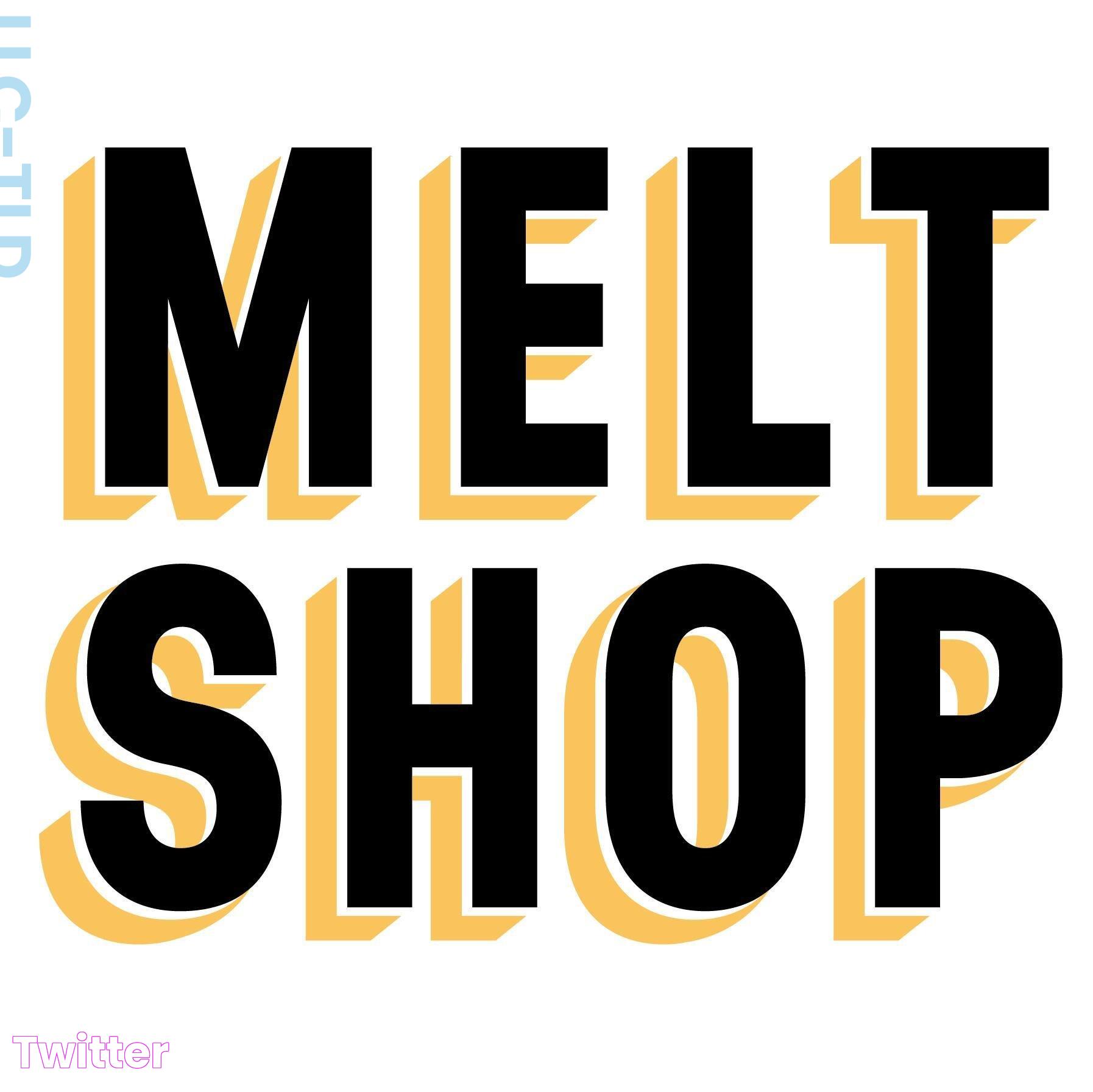
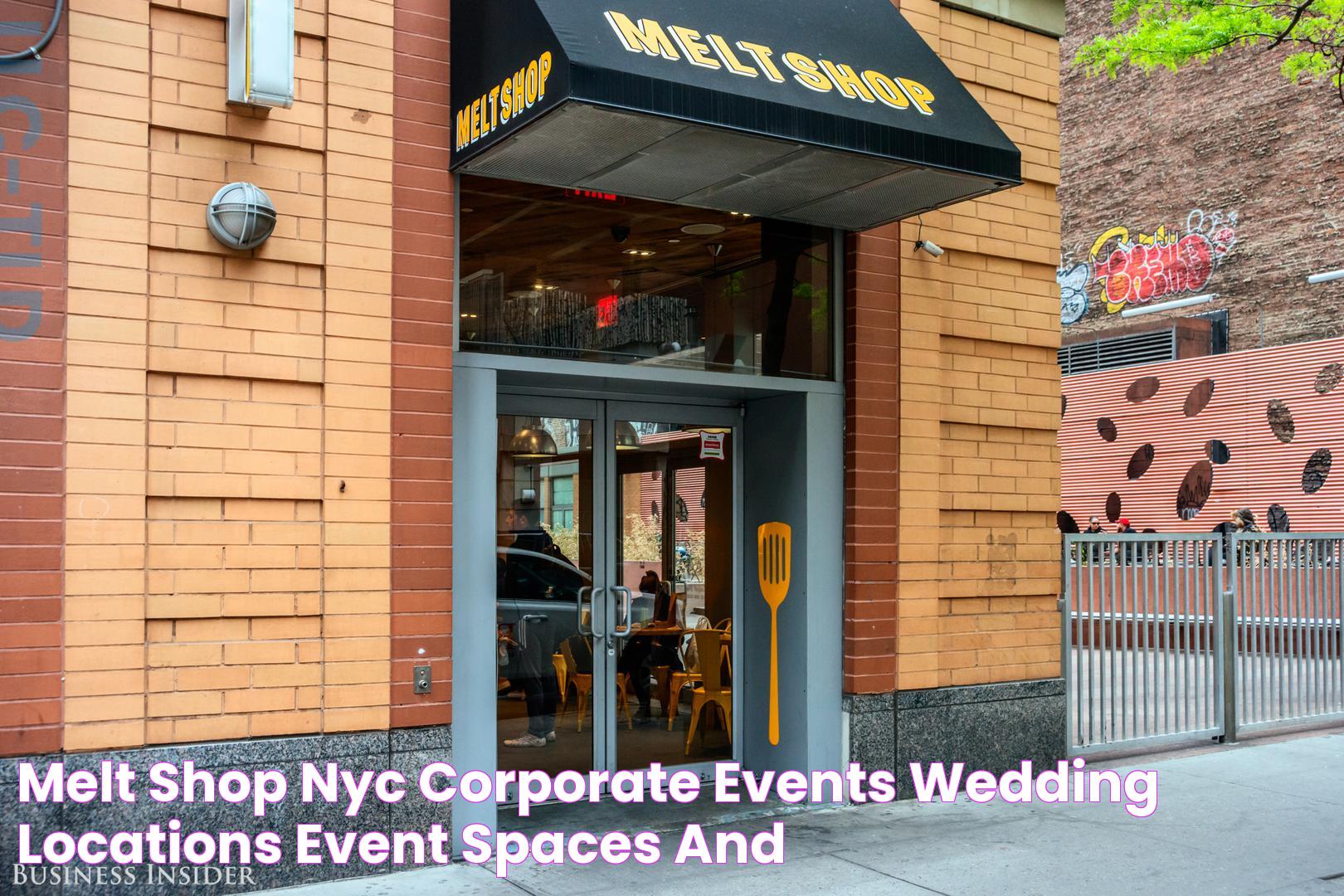